導入 MES 並跨越整合 ERP 的障礙
成功案例 - 世界級印表機的開發生產商
面對消費市場的詭譎變化,這家國際級企業需要更具競爭力的整合性 MES 解決方案
客戶背景
該公司是一家國際級的企業,著重於研發使列印更便利的方法。自1991年以來,一直致力於開發簡單易用的商用及家庭用雷射印表機、噴墨印表機、及耗材的服務。
其海外後端組裝廠員工共計約2,000多名,全部的產線每日可生產多達 12 萬瓶墨水,目前這個工廠擁有每年約4,000多萬瓶的產量。
該企業積極採納了亞太地區及全球客戶的回饋,並將技術轉化為極具競爭力的產品和解決方案,也因此極需一套整合性的 MES 系統,來面對市場詭譎變化,以達到讓商品生產供應速度恰好合乎市場需求的目標。
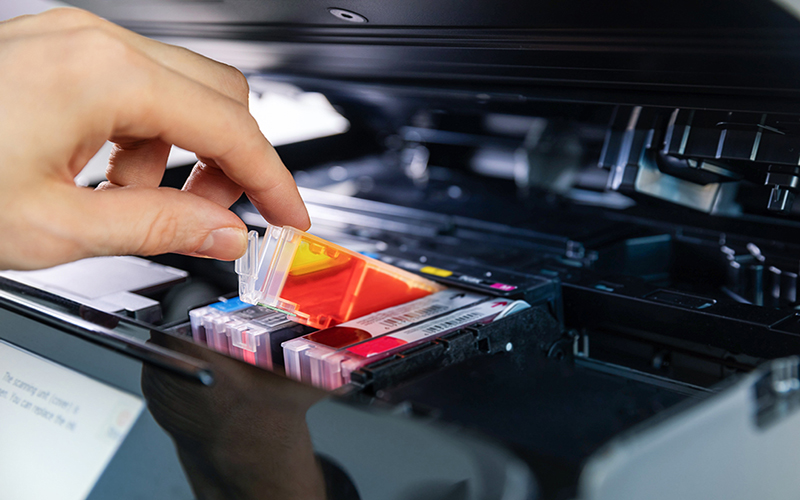
需求與面臨的挑戰
該公司整理出 5 大需求為本次專案需要達成之目標 :
- 1. 完整追蹤所有物料及墨水匣成品紀錄
- 2. 生產資訊連接至 ERP
- 3. 計算墨水匣自動生產線之 OEE
- 4. 減少生產線上紙張使用
- 5. 加強產品品質管理
在為客戶導入系統前,我們會先評估哪幾條重要的生產線必需先行施作。經驗與結果顯示,如此可以讓工單的執行更有效率。
而在 MES 與 ERP 的整合 – 第一步我們會去調查,針對哪一項工作進行改善最有可能帶來最顯著的效果。因此我們分析該企業總部及生產單位人員的需求,而這些資料將會成為未來解決方案的架構基礎。
面臨的 3 大挑戰 :
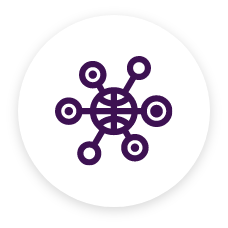
如何強化作業流程
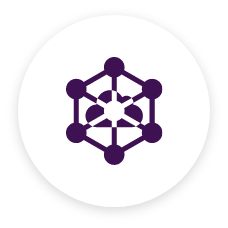
整合生產線上資訊
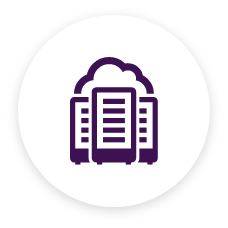
ERP 和 MES 的整合
專案過程
第一部份 - 資料蒐集及機台資料呈現
第一部分為統合所有的生產項目並建立生產模型,以便所有生產線人員可以容易地查看他們作業所需的區段,同時滿足原物料過站追蹤的需求。
為因應生產線需求,該公司決定全力扶持新系統導入並提供高效能伺服器設備及穩定的網路基礎架構。 為整合現場生產與企業總部之間的異質系統,軟體部分採用 AVEVA System Platform 和 AVEVA InTouch HMI ,提供現場資訊整合的平台的同時擁有強大的視覺化圖控功能;
而 AVEVA Information Server 的角色則提供強大的 Web Report 功能。有了如此彈性化的系統平台,日後 MES 模組可非常輕易地整合 ERP 和監控層資訊。
以功能面來看,使用者可以直接受惠於自動產出的物料文件進而達到追蹤的目的。自動將生產工單轉入之後的 MES 系統搭配一鍵產出的報表,可即時得知實際庫存狀況及物料供給狀況。
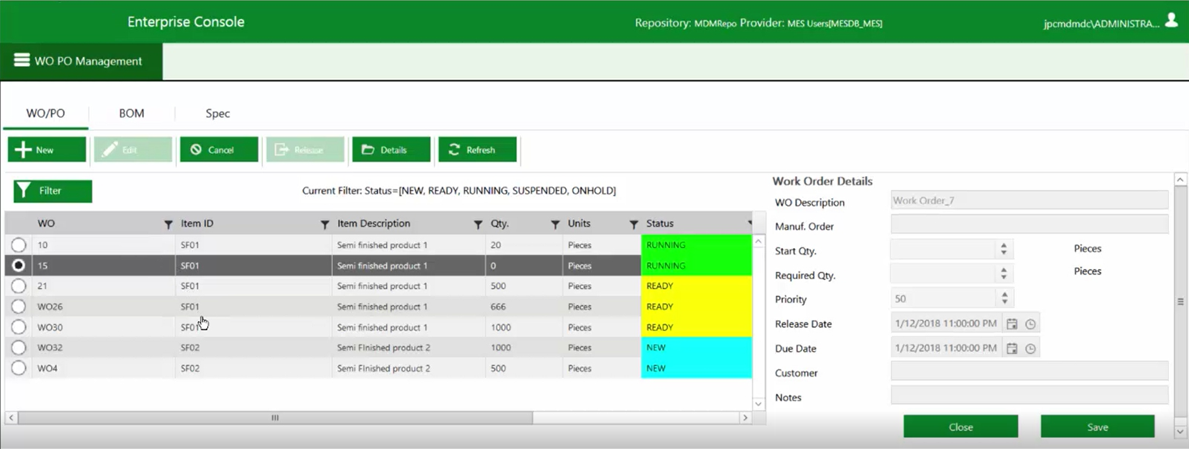
MES 自動將每個從 ERP 來的生產工單進行排序,同時比對 BOM 表
 
第二部份 - 導入 MES 系統
在此階段中,第一個步驟便是建立物料流,定義各物料、工作站如墨水匣準備站、墨水匣組裝站及墨水匣填充站及成品包裝區,最後再定義 1,000 種以上的產品及其組成原物料。
在此階段的工作牽涉到 ERP 和 MES 雙向資料的交換。在接到生產工單後, ERP 系統會自動將生產工單拆解成現場可執行的工單投入 MES 系統中輸入適當的生產數量。而由 MES 系統自動分配到各生產線的工單可以在工作站中查看。
當工單完成後,MES 會將成品的相關資訊回拋 ERP 系統中。每一個生產的環節皆被系統所管控,例如:在墨水匣準備站的相關資料如數量若不符合規則,或是前一階段的工作未完成,則無法進入下一生產階段。減少人員發生錯誤及警告錯誤資料使用的機會,瑕疵報廢品也因此減少,達成生產成本降低的目標。
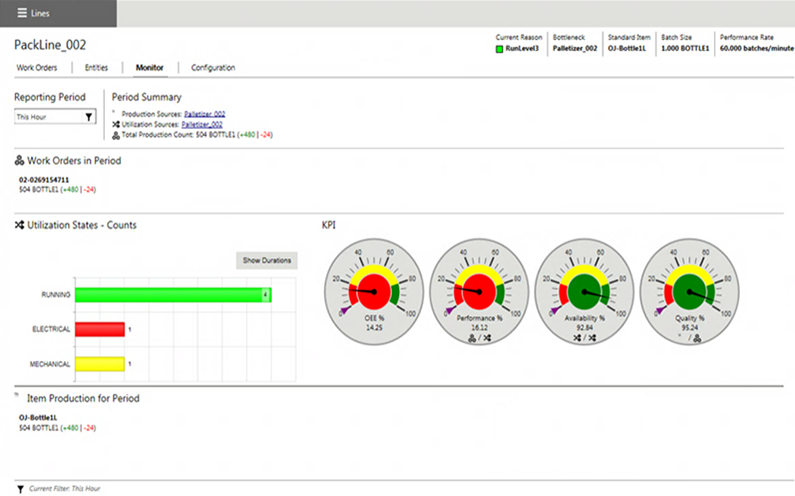
MES 系統會自動統計產線的OEE,並以圖表化的方式呈現
 
第三部分 - 為每個產線設下 KPI
當 MES 系統順利導入後,最後一個部分則是在自動生產線上加入 AVEVA MES 特有的功能模組 : Performance 模組。當定義好 Performance 模組中的 KPI 項目後,這些指標就可被即時監控,並可針對不達 KPI 的產線迅速作出調整對策。
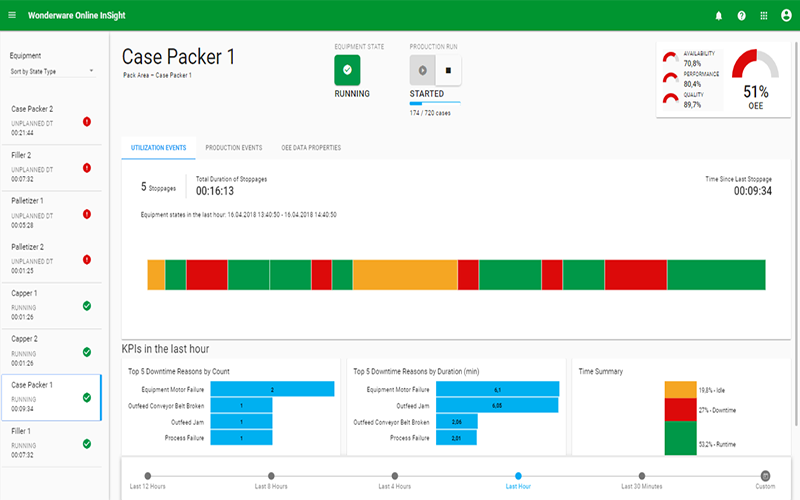
除了產線的 OEE ,MES 還能監控個別生產機台的 KPI,同樣利用容易判斷的圖表化方式呈現
 
系統架構
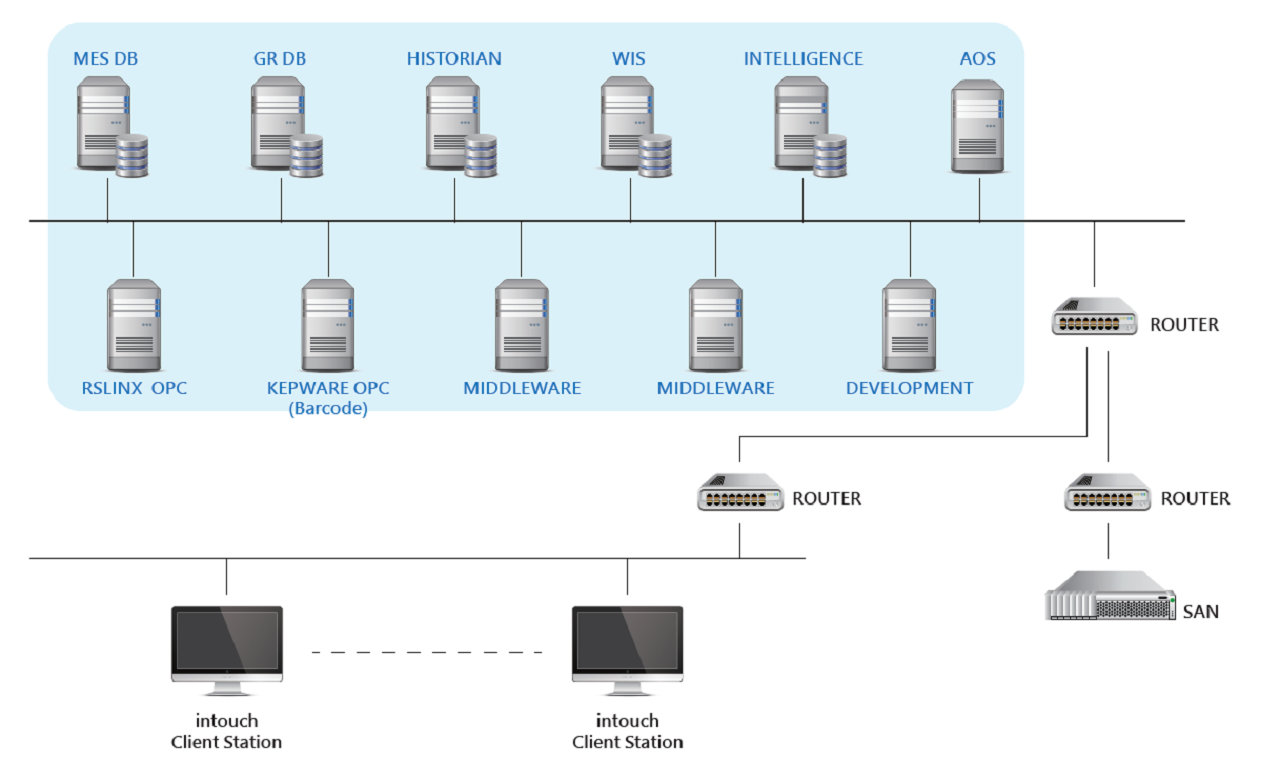
透過 AVEVA System Platform ,將現場製程控制系統、生產資料庫、MES系統之間無縫整合,同時順利將數據上拋至 ERP 系統
成果
OT 系統與 IT 系統整合後,身為決策者的我們更容易進一步做到跨區域的分析,並且找到去除生產瓶頸的策略 ---- 廠務經理
導入 MES 系統後可以讓我們看到整個生產流程的全貌,包含生產用料、機台狀況、警報及歷史 資料等... 這些資料都可匯整提供到 ERP,將手動處理及文件列印需求量降到最低,減少人為疏失,進而降低成本。經理人可以隨時得知機台預計產量,確實掌握工單排程。
而另一重要功能為,MES 可整合 ERP 做到即時庫存監控。從客戶端接收到訂單當下,便可直 接對應到 BOM 表,BOM 表即可同步確認庫存是否充足。
OT 與 IT 系統的整合,不僅可以讓我們取得更詳細的資料,並且一次分析不同的生產過程。從企業的角度觀之,更可確認整體的效益、規劃策略及成本;從生產的角度而言,也可輕鬆觀察到生產機台使用率、停機及生產時間等問題。
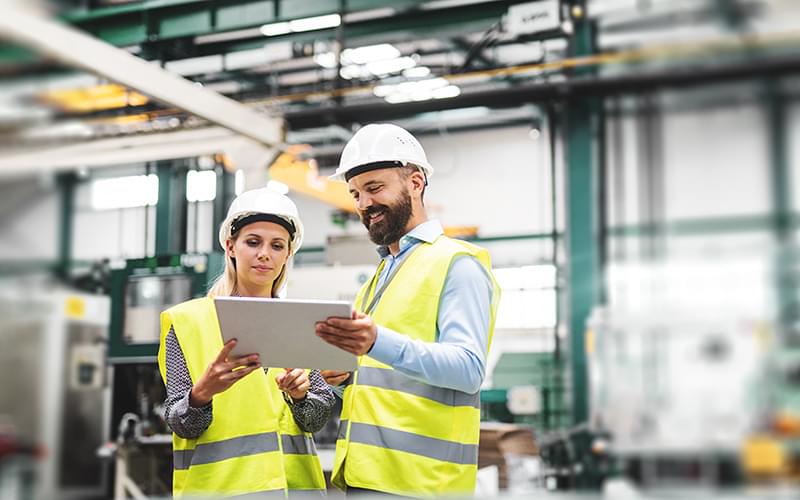
 
此專案主要使用產品
了解更多成功案例
Success Stories
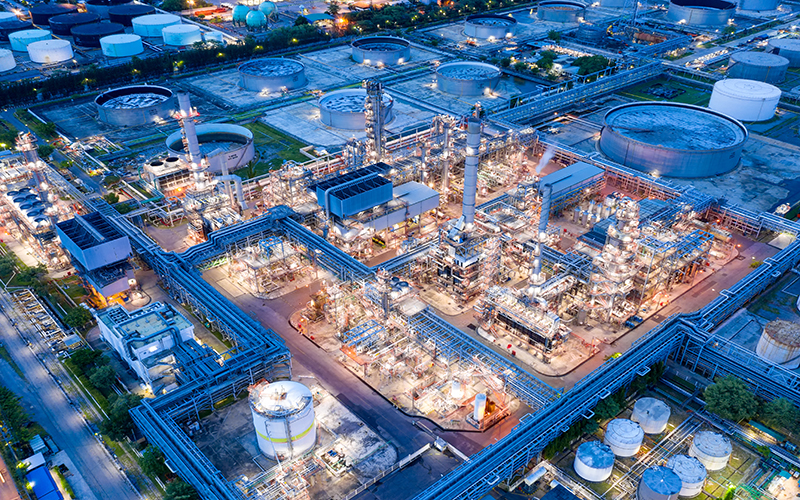
化學廠系統建置與整合
通透全廠系統與數據數位化工廠的經典案例
此案為台商投資新建在中國昆山的高純度電子化學廠,一年純化及分裝化學品約 49200噸。
System Platform 平台消除了工業應用開發的複雜度,數據集中管理,形成一個即時資料中心。支援多人開發的功能,使程式設計團隊可以同時在同一個系統平台執行
「提供非常符合實際工廠的架構,簡化系統維護能力,最小化人員傳統抄表的需要,有效運用人力資源。」 ---- 廠長